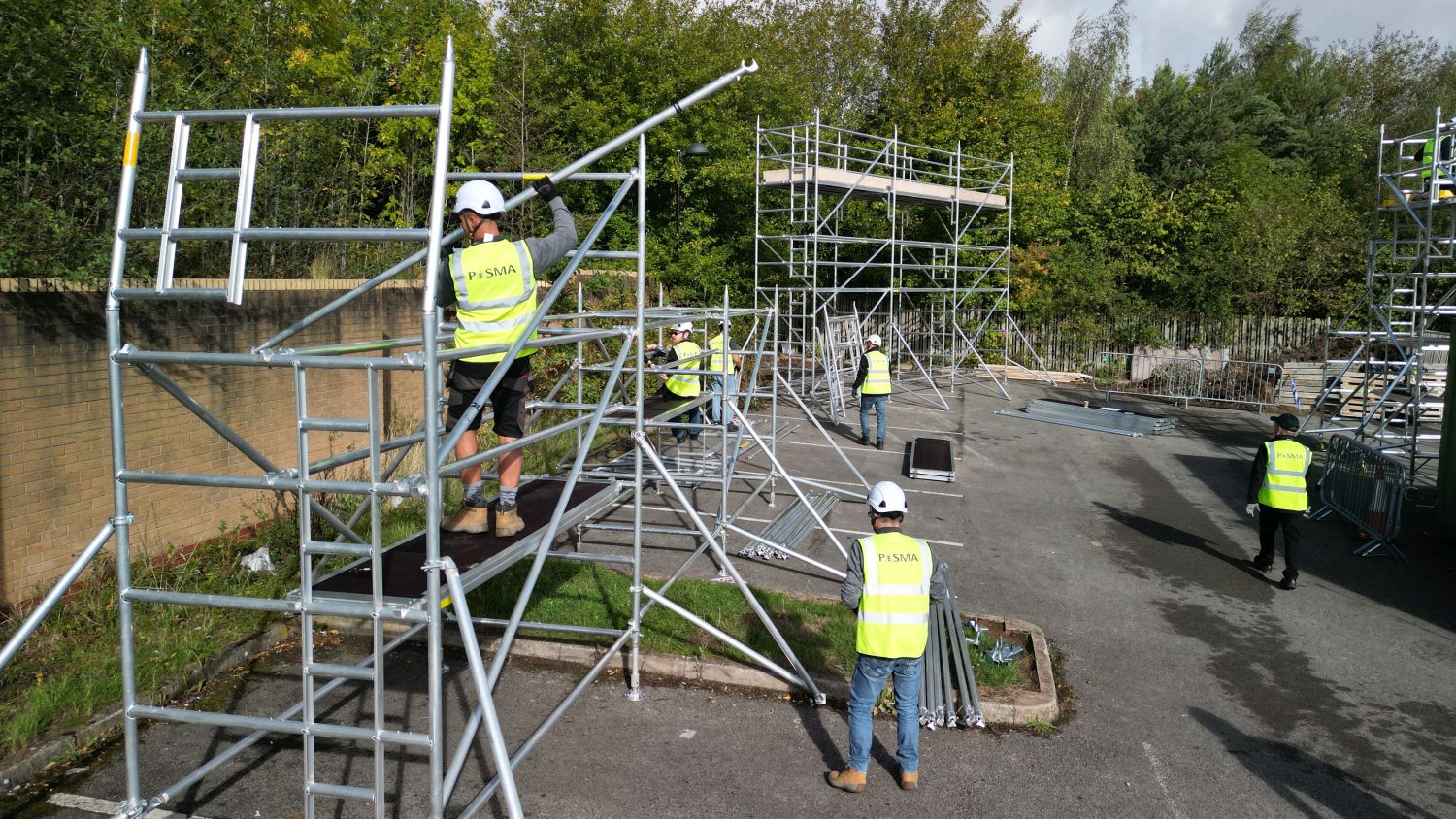
Is every access tower safe? And if not, how do you choose one that is? Don Aers shares five steps to make sure you’ve got a tower you can climb confidently.
When you need a quick, lightweight, flexible piece of access equipment, a tower often fits the bill. They’re a safe way to work at height, with collective fall prevention included from start to finish.
1. Pick the right tower for the job
Firstly, don’t just grab the nearest tower and hope it’ll do! Instead, take care to choose one that’s appropriate for the task, considering factors such as:
- Platform height – does it reach where you need to be?
- Configuration – for example, if you’re working over a staircase use a stepped tower and for a long, uninterrupted deck area pick linked or bridged towers
- Material – choose GRP (fibreglass) to reduce (but not eliminate) the risks of electrocution when working near electrical sources
You can take advice from manufacturers, suppliers or hire centres on this.
2. Check it meets safety standards
Towers should be certified to EN 1004-1 or BS 1139-6, meaning they meet minimum safety requirements such as:
- Purpose designed platforms with safe trapdoor entry and exit
- Built in access for safe ascent and descent
- Supplied with the correct size and quantity of stabilisers to prevent overturning
- The correct number of guardrails with the correct gaps and dimensions to prevent a fall
EN 1004 covers single bay freestanding towers on wheels. Everything else is covered by BS 1139-6. PASMA members will only make or supply towers that meet the latest standards.
3. Get trained
Towers can only be safely assembled, inspected, used or dismantled if the worker is competent.
Anyone working with access towers should – at a minimum – have completed a PASMA Towers for Users training course. Additional training is required for anything more complex than an EN 1004 mobile access tower. Their managers and supervisors should complete PASMA Towers for Managers.
There’s a network of approved training centres who can book these courses for you.
4. Follow the manual
Trained operatives should always follow the instruction manual provided by the manufacturer or hire company. It’s a legal requirement for this document to be available on site and that’s because it contains critical safety information needed to build the tower correctly.
5. Inspect your towers
Tower components can become damaged or worn over time, so always check to make sure they’re in good working condition before you assemble the tower.
Then, inspect the completed structure before you start work. Remember, it’s only safe to use if it’s been built correctly, so take the time to double check. PASMA’s new TowerSure app guides you through inspections step-by-step and automatically stores the inspection record centrally so the rest of the team can access it quickly and easily.
With those steps covered, you’ll have the peace of mind you need to climb up and get on with the job at hand.
Don Aers is technical director at PASMA